Acero: Una larga historia con múltiples aplicaciones
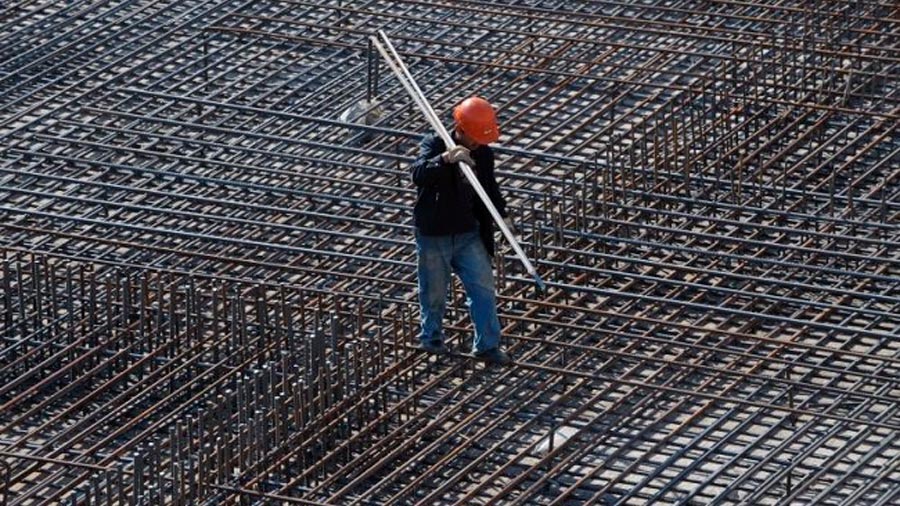
En Lampadia pretendemos crear conciencia sobre sobre el mundo de nuestros días. Nuestro objetivo es propiciar que los peruanos optemos por una sólida economía de mercado, y eso conlleva, entre otras cosas, analizar la creación de ideas en el mundo global; ‘diseccionar’ los desarrollos económicos, separándolos de los ropajes ideológicos; difundir el potencial de desarrollo del Perú, retirando la contaminación de la política partidista; destacar nuestras riquezas y nuestra capacidad de superar nuestras limitaciones.
En ese proceso, hemos hecho especial hincapié en defender la importancia del desarrollo de nuestros recursos naturales, como la mejor oportunidad de crear riqueza en el volumen y la oportunidad, que nos permitan nivelarnos aprisa, con los países más avanzados, de cara a la ‘cuarta revolución industrial’.
Varias veces hemos destacado la magnífica y sorprendente conversión de la industria peruana, que hoy, sin protección del Estado, es competitiva y exportadora, y está integrada a los sectores primarios. Su tamaño con respecto al PBI del país, alrededor de un 14%, es nominalmente del mismo orden, desde la ominosa época de la ‘sustitución de importaciones’. Sin embargo, su tamaño efectivo es mucho mayor que el de la era del proteccionismo, pues, hoy día su aporte al PBI no incluye aranceles altos, ni márgenes de utilidad sobredimensionados de industriales protegidos.
Fuente: INVDES
A continuación, presentamos información ilustrativa sobre el acero, el material industrial de mayor uso en el mundo moderno, que pensamos vale la pena compartir con nuestros lectores:
I. Aprendiendo sobre el acero
Su historia desde la Edad del Hierro hasta los hornos de arcos eléctricos
Imágenes de Buena Vista / Stone / GettyImages
Terence Bell
The Balance
21 de agosto de 2017
Traducido y glosado por Lampadia
El desarrollo del acero se remonta a más de 4,000 años, desde el comienzo de la Edad del Hierro. Demostrando ser más duro y más fuerte que el bronce, que anteriormente había sido el metal más utilizado, el hierro comenzó a desplazar al bronce en armamentos y herramientas.
Durante los siguientes miles de años, sin embargo, la calidad del hierro producido dependería tanto del mineral disponible como de los métodos de producción.
En el siglo XVII, se entendían bien las propiedades del hierro, pero la creciente urbanización en Europa exigía un metal estructural más versátil.
Y en el siglo XIX, la cantidad de hierro consumido por la expansión de los ferrocarriles proporcionó a los metalúrgicos el incentivo financiero para encontrar una solución a la fragilidad del hierro y los ineficientes procesos de producción.
Sin duda, sin embargo, el gran avance en la historia del acero se produjo en 1856 cuando Henry Bessemer desarrolló una forma efectiva de usar oxígeno para reducir el contenido de carbono en el hierro: así nació la industria siderúrgica moderna.
La era del hierro
A temperaturas muy altas, el hierro comienza a absorber carbono, disminuyendo el punto de fusión del metal, lo que resulta en hierro fundido (2.5% a 4.5% de carbono). El desarrollo de los altos hornos, utilizados por primera vez por los chinos en el siglo VI a.C., pero más ampliamente utilizados en Europa durante la Edad Media, aumentó la producción de hierro fundido.
El arrabio es el hierro fundido que sale de los altos hornos y se enfría en un canal principal. Los lingotes grandes, centrales y contiguos se parecían a una cerda y a sus lechones lactantes.
El hierro fundido es fuerte pero sufre fragilidad debido a su contenido de carbono, por lo que no es ideal para trabajar y dar forma. Como los metalúrgicos se dieron cuenta de que el alto contenido de carbono en el hierro era fundamental para el problema de la fragilidad, experimentaron con nuevos métodos para reducir el contenido de carbono con el fin de hacer que el hierro sea más viable.
A fines del siglo XVIII, los fabricantes de hierro aprendieron cómo transformar el arrabio fundido en un hierro forjado de bajo contenido de carbono utilizando hornos de pudelaje (desarrollado por Henry Cort en 1784). Los hornos calentaron el hierro fundido, que tuvo que ser removido por la pudelación usando herramientas largas en forma de remos, permitiendo que el oxígeno se combinara y eliminara lentamente el carbono.
A medida que disminuye el contenido de carbono, aumenta el punto de fusión del hierro, por lo que las masas de hierro se aglomeran en el horno. Estas masas serían removidas y trabajadas con un martillo de forja por el pudelaje antes de ser enrolladas en hojas o rieles. En 1860, había más de 3,000 hornos de pudelaje en Gran Bretaña, pero el proceso seguía obstaculizado por su intensidad de trabajo y combustible.
Una de las primeras formas de acero, acero blister, comenzó su producción en Alemania e Inglaterra en el siglo XVII y se produjo al aumentar el contenido de carbono en el arrabio fundido mediante un proceso conocido como cementación. En este proceso, las barras de hierro forjado se cubrieron con carbón en polvo en cajas de piedra y se calentaron.
Después de aproximadamente una semana, el hierro absorberá el carbono del carboncillo. El calentamiento repetido distribuiría el carbono de manera más uniforme y el resultado, después del enfriamiento, era el acero blíster. El mayor contenido de carbono hizo que el acero blíster sea mucho más viable que el arrabio, porque puede ser planchado o enrollado.
La producción de acero blíster avanzó en la década de 1740 cuando el relojero inglés Benjamin Huntsman, al tratar de desarrollar un acero de alta calidad para sus manantiales, descubrió que el metal podía fundirse en crisoles de arcilla y perfeccionarse con un flujo especial para eliminar la merma que dejaba el proceso de cementación. El resultado fue crisol o acero fundido. Pero debido al costo de producción, tanto el blister como el acero fundido solo se usaron en casos especiales.
Como resultado, el hierro fundido hecho en hornos de pudelaje permaneció como el metal estructural primario en la industrialización de Gran Bretaña durante la mayor parte del siglo XIX.
El proceso de Bessemer y la fabricación de acero moderna
El crecimiento de los ferrocarriles durante el siglo XIX, tanto en Europa como en EEUU, ejerció una gran presión sobre la industria del hierro, que aún luchaba con ineficientes procesos de producción.
Sin embargo, el acero aún no estaba probado como metal estructural y la producción era lenta y costosa. Fue hasta 1856 cuando Henry Bessemer ideó una forma más efectiva de introducir oxígeno en el hierro fundido para reducir el contenido de carbono.
Conocido ahora como el Proceso de Bessemer, Bessemer diseñó un receptáculo en forma de pera, conocido como “convertidor”, en el que se podía calentar hierro mientras se podía aspirar oxígeno a través del metal fundido. A medida que el oxígeno pasaba a través del metal fundido, reaccionaría con el carbono, liberando dióxido de carbono y produciendo un hierro más puro.
El proceso fue rápido y barato, eliminando el carbono y el silicio de hierro en cuestión de minutos, pero sufrió por ser demasiado exitoso. Se eliminó demasiado carbono y quedó demasiado oxígeno en el producto final. Bessemer finalmente tuvo que reembolsar a sus inversores hasta que pudo encontrar un método para aumentar el contenido de carbono y eliminar el oxígeno no deseado.
Casi al mismo tiempo, el metalúrgico británico Robert Mushet adquirió y comenzó a probar un compuesto de hierro, carbono y manganeso, conocido como speigeleisen. Se sabía que el manganeso eliminaba el oxígeno del hierro fundido y el contenido de carbono en el speigeleisen, si se añadía en las cantidades adecuadas, proporcionaría la solución a los problemas de Bessemer. Bessemer comenzó a agregarlo a su proceso de conversión con gran éxito.
Sin embargo, aún quedaba un problema. Bessemer no había logrado encontrar una forma de eliminar el fósforo, una impureza perjudicial que hace que el acero sea frágil, de su producto final. En consecuencia, solo se podía usar mineral libre de fósforo de Suecia y Gales.
En 1876, el galés Sidney Gilchrist Thomas propuso la solución añadiendo un flujo químicamente básico de piedra caliza al proceso de Bessemer. La piedra caliza sacó fósforo del arrabio en la merma, permitiendo que se elimine el elemento no deseado.
Esta innovación significó que, finalmente, el mineral de hierro de cualquier parte del mundo podría usarse para fabricar acero. No sorprende que los costos de producción de acero comenzaron a disminuir significativamente. Los precios del ferrocarril de acero cayeron más del 80% entre 1867 y 1884, como resultado de las nuevas técnicas de producción de acero, iniciando el crecimiento de la industria siderúrgica mundial.
El proceso de ‘hogar abierto’
En la década de 1860, el ingeniero alemán Karl Wilhelm Siemens mejoró aún más la producción de acero a través de su creación del proceso de hogar abierto. El proceso de hogar abierto produjo acero de arrabio en grandes hornos poco profundos.
Usando altas temperaturas para quemar el exceso de carbono y otras impurezas, el proceso se basó en cámaras de ladrillo calentadas debajo del hogar. Los hornos regenerativos luego usaron gases de escape del horno para mantener altas temperaturas en las cámaras de ladrillo.
Este método permitió la producción de cantidades mucho mayores (se podían producir 50-100 toneladas métricas en un horno), pruebas periódicas del acero fundido de modo que se pudiera fabricar para cumplir especificaciones particulares y el uso de chatarra de acero como materia prima. Aunque el proceso en sí mismo fue mucho más lento, en 1900 el proceso de hogar abierto había reemplazado en gran medida el proceso de Bessemer.
El nacimiento de la industria siderúrgica
La revolución en la producción de acero que proporcionó material más barato y de mayor calidad, fue reconocida por muchos empresarios de la época como una oportunidad de inversión. Los capitalistas de finales del siglo XIX, incluidos Andrew Carnegie y Charles Schwab, invirtieron e hicieron millones (miles de millones en el caso de Carnegie) en la industria siderúrgica. Carnegie’s US Steel Corporation, fundada en 1901, fue la primera corporación valorada en más de mil millones de dólares.
Fabricación de acero con hornos de arco eléctrico
Justo después del cambio de siglo, ocurrió otro desarrollo que tendría una fuerte influencia en la evolución de la producción de acero. El horno de arco eléctrico (EAF) de Paul Heroult fue diseñado para pasar una corriente eléctrica a través del material eléctrico, dando como resultado una oxidación exotérmica y temperaturas de hasta 3272 ° F (1800 ° C), más que suficiente para calentar la producción de acero.
Utilizados inicialmente para aceros especiales, los EAF crecieron en uso y, en la Segunda Guerra Mundial, se utilizaron para la fabricación de aleaciones de acero. El bajo costo de inversión involucrado en la instalación de las plantas de EAF les permitió competir con los principales productores estadounidenses como US Steel Corp. y Bethlehem Steel, especialmente en aceros al carbono o productos largos.
Debido a que los EAF pueden producir acero a partir de chatarra al 100% o de alimentos ferrosos fríos, se necesita menos energía por unidad de producción. A diferencia de los hogares básicos de oxígeno, las operaciones también pueden detenerse e iniciarse con un pequeño costo asociado. Por estos motivos, la producción a través de los EAF ha ido aumentando de manera constante durante más de 50 años y ahora representa alrededor del 33% de la producción mundial de acero.
Siderúrgica de Oxigeno
La mayoría de la producción global de acero, aproximadamente el 66%, ahora se produce en instalaciones básicas de oxígeno. El desarrollo de un método para separar el oxígeno del nitrógeno a escala industrial en la década de 1960 permitió grandes avances en el desarrollo de hornos básicos de oxígeno.
Los hornos de oxígeno básicos soplan oxígeno en grandes cantidades de hierro fundido y desecho de acero y pueden completar una carga mucho más rápidamente que los métodos de hogar abierto. Los buques grandes con hasta 350 toneladas métricas de hierro pueden completar la conversión al acero en menos de una hora.
La eficiencia de costos de la fabricación de acero al oxígeno hizo que las fábricas de hogares abiertos no fueran competitivas y, luego de la llegada de la producción de acero al oxígeno en la década de 1960, las operaciones de hogar abierto comenzaron a cerrarse. La última instalación de hogar abierto en los Estados Unidos cerró en 1992 y en China en 2001.
II. Perfil de metal: todo sobre el acero
Thierry Dosogne / GettyImages
Terence Bell
The Balance
02 de marzo de 2017
Traducido y glosado por Lampadia
Steel (acero), el material de construcción más importante del mundo, es una aleación de hierro que contiene entre 0.2% y 2 % de carbono en peso.
Historia
El advenimiento de la producción de acero comercial a fines del siglo XIX fue el resultado de la creación de Sir Henry Bessemer de una manera eficiente de reducir el contenido de carbono en el hierro fundido. Al reducir la cantidad de carbono en el hierro a aproximadamente el 2%, se produce la aleación más dura y más maleable.
Producción
Hoy en día, la mayoría de los productos de acero son producidos por métodos básicos de oxígeno (también conocidos como producción básica de oxígeno o BOS). BOS se denomina así porque requiere que el oxígeno se inyecte en grandes recipientes que contienen hierro fundido y chatarra de acero.
Aunque BOS representa la mayor parte de la producción mundial de acero, el uso de hornos de arco eléctrico (EAF) ha ido en aumento desde principios del siglo XX y ahora representa alrededor de un tercio de toda la producción de acero.
Grados
Existen más de 3,500 diferentes grados de acero. El acero comercial generalmente se clasifica en cuatro grupos según su contenido de aleación de metal y aplicaciones de uso final:
1. Aceros de carbono (incluidos los aceros de bajo carbono, de medio carbono y de alto carbono)
2. Aceros de aleación (metales comunes de aleación, manganeso, silicio, níquel y cromo)
3. Aceros Inoxidables (contienen aproximadamente 10% de cromo y clasificados como austeníticos, ferríticos y martensíticos)
4. Aceros para herramientas (aleados con metales duros y de alta temperatura, como molibdeno y tungsteno)
El acero tiene una amplia gama de composiciones de aleación, que le permiten tener diversas propiedades mecánicas.
Propiedades
Se producen diferentes tipos de acero de acuerdo con las propiedades requeridas para su aplicación, y se usan diversos sistemas de clasificación para distinguir los aceros basados en estas propiedades. La siguiente tabla enumera las propiedades de los aceros a temperatura ambiente (25 ° C).
Aplicaciones
Desde aceros inoxidables y de alta temperatura hasta productos de carbono planos, las diversas formas y aleaciones de acero ofrecen diferentes propiedades para satisfacer una amplia gama de aplicaciones. Por estas razones, así como la combinación de metal de alta resistencia y un costo de producción relativamente bajo, el acero ahora se usa en innumerables productos.
Las aplicaciones de acero se pueden dividir en cinco sectores.
III. Aplicaciones de acero
¿Para qué se usa el acero?
ThanathamPiriyakarnjanakul / EyeEm / GettyImages
Terence Bell
The Balance
20 de agosto de 2017
Traducido y glosado por Lampadia
El acero es el material de metal más utilizado y reciclado en la tierra. Desde aceros inoxidables y de alta temperatura hasta productos de carbono planos, el acero en sus diversas formas y aleaciones ofrece diferentes propiedades para satisfacer una amplia gama de aplicaciones. Por estas razones, así como la combinación de metal de alta resistencia y un costo de producción relativamente bajo, el acero ahora se usa en innumerables productos.
Las aplicaciones de acero se pueden dividir en cinco sectores:
1. Construcción
2. Transporte
3. Energía
4. Embalaje
5. Electrodomésticos e industria
Construcción:
La mayoría del acero va a la industria de la construcción. Las estructuras de acero sostenibles se pueden construir rápidamente a un precio bajo. El acero, en sus diversas formas y aleaciones, puede diseñarse para cumplir los requisitos de proyectos únicos, que le permiten incorporarse a la infraestructura en todos los entornos. Dependiendo de las condiciones a las que esté expuesta la estructura, el acero puede alearse o tratarse superficialmente de forma diferente para protección.
El desarrollo de técnicas eficientes de producción de acero a finales del siglo XX contribuyó al crecimiento de los ferrocarriles en todo el mundo, así como a la llegada del edificio de gran altura. Muchas estructuras históricas famosas, como el EmpireStateBuilding, contienen acero como material de construcción primario.
El acero también se puede encontrar en:
- edificios bajos y altos
- edificio educativos y hospitalarios
- estadios deportivos y estaciones
- concreto reforzado
- placas de la cubierta de puentes
- muelles y cables de suspensión
- puertos
- revestimiento y techos
- oficinas
- túneles
- vallado de seguridad
- defensas costeras e inundaciones
Transporte:
Los aceros de ingeniería son aceros forjados que están diseñados para tener ciertos niveles específicos de elasticidad, resistencia, ductilidad y resistencia a la corrosión. Se utilizan en los sectores de ingeniería y fabricación en general, pero el grueso se destina al transporte de vehículos.
El acero representa más del 50% del peso de un automóvil promedio. Los aceros avanzados de alta resistencia (AHSS) se utilizan en vehículos. Es un material ligero que requiere menos energía para producir y reduce las emisiones de CO2.
Se utilizan diferentes tipos de acero para la carrocería, las puertas, el motor, la caja de cambios, la dirección, la suspensión, los ejes de las ruedas y el interior.
Además del mercado automotriz, el acero se encuentra en materiales de transporte como:
- camiones
- transmisiones
- trenes
- rieles
- naves
- cadenas de anclaje
- trenes de aterrizaje de aeronaves
- componentes de motores a reacción
Energía:
Todos los segmentos del sector de la energía, incluida la nuclear, eólica, eléctrica y de gas natural, demandan acero para infraestructura. El acero también se utiliza para la extracción de recursos, como en plataformas marinas, equipos de movimiento de tierras y canteras, grúas y carretillas elevadoras. Debido a los exigentes entornos, los aceros al carbono, microaleados, de alta resistencia y los aceros inoxidables se utilizan en la producción de plataformas y tuberías mar adentro.
Además de estos, muchos otros proyectos de energía dependen de grandes cantidades de acero:
- pozos y plataformas de petróleo y gas
- tuberías
- componentes de turbina de energía eléctrica
- pilones de electricidad
- turbinas de viento
- torres de transmisión
- electroimanes
- escudos electromagnéticos
Embalaje:
El embalaje de acero protege los productos del agua, aire y la exposición a la luz, y es totalmente reciclable. Este método de almacenamiento ha existido por más de 200 años.
El acero permite el llenado de alta velocidad y el empaque liviano y fácil de abrir. Los aceros de empaque a menudo están hechos de una tira de acero laminado en frío de bajo carbono y tienen un acabado superficial. El acero está estañado para evitar la corrosión y luego se recubre con un polímero, se laca e imprime. La mayoría de los envases de acero se destinan al envasado de alimentos y bebidas, seguido de una línea general, aerosoles y cierres (por ejemplo, tapas de botellas).
Electrodomésticos e Industria:
Alrededor del 75% del peso de los electrodomésticos típicos proviene del acero. El acero se encuentra en electrodomésticos como neveras, lavadoras, hornos, microondas, fregaderos, cubiertos, etc.
El acero también cuenta con muchos bienes de la industria, como vehículos agrícolas y maquinaria, tanques de almacenamiento, herramientas, estructuras, pasarelas y equipos de protección.
Lampadia